THE JOURNAL
New to MR PORTER’s fine-watch portfolio, Jaeger-LeCoultre is the Swiss house the other watchmakers rely upon.
Save for a few ski lifts, the view from Mr Antoine LeCoultre’s workbench has barely changed in more than 180 years. Perched by the limpid shores of the Lac de Joux, it gazes across the sweeping south slopes of the Vallée de Joux, soundtracked by the constant clank of cowbells. It’s a cliché to say “chocolate box”, but this really is the sort of place that Switzerland’s confectioners look for brand direction.
It was here in this secluded fold of the Jura Mountains, 1,000ft up, that the 19th century’s local dairy farmers found themselves cut off during every harsh winter. To diversify, they started to mine small amounts of ore from the surrounding hills, experimenting in intricate metalwork. And eventually, watchmaking.
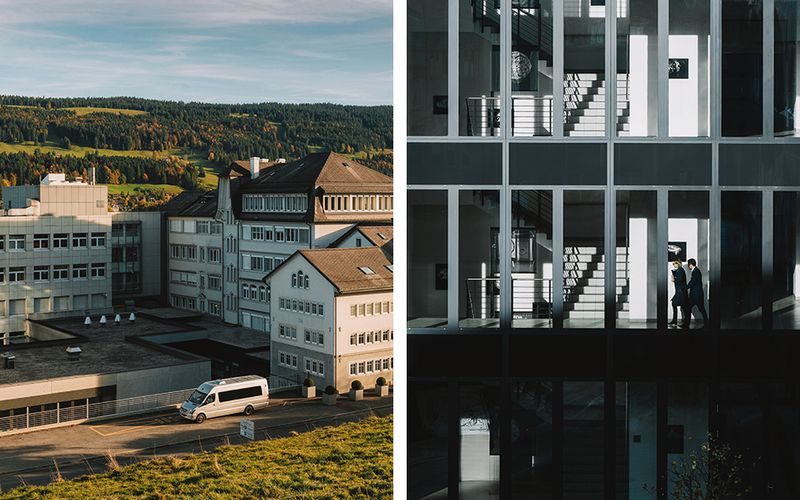
In 1833, Mr LeCoultre was the very first to establish a factory here, kickstarting the Joux’s renowned speciality for particularly high-end, complicated horology, and it wasn’t long before the valley became the epicenter of innovative Swiss watchmaking – the Silicon Valley of its day. Audemars Piguet, Blancpain, Patek Philippe and Vacheron Constantin are all neighbours, but Jaeger-LeCoultre remains the ultimate “Watch Valley” brand; the Watchmaker of Watchmakers.
It has supplied calibres and components to all the above, and in the days when the snow still meant lockdown, the great and the good of Geneva’s ateliers, just 60km down the other side of the slopes, would have to pray they’d stocked up enough LeCoultre components to last the long winter.
And this was all down to Mr LeCoultre’s pioneering efforts consolidating every watchmaking trade beneath a single roof. Today, it’s a lot more than a single roof, but the sprawling campus of squeaky-clean factory buildings is still on the exact same site as Mr LeCoultre’s original farmhouse-turned-workshop (now the spot housing the brand’s “Heritage Gallery” of masterpieces, from 1907’s wafer-thin Calibre 145 to 1931’s immortal Art Deco classic, the flip-cased Reverso).
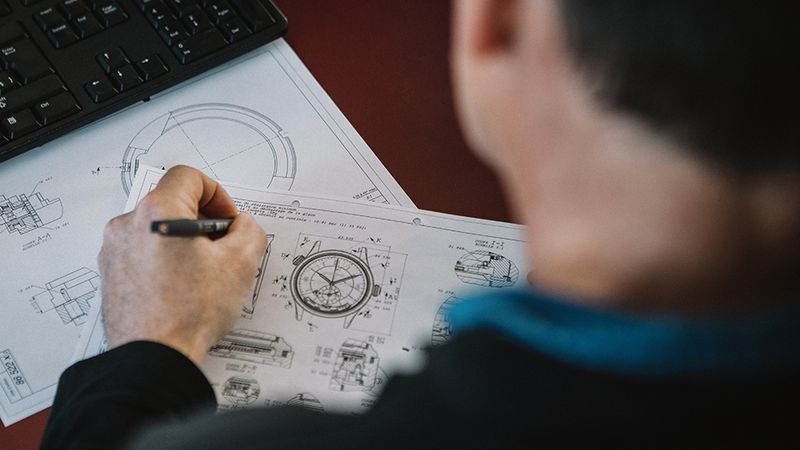
Extraordinarily, “La Grande Maison” has now mastered as many as 180 individual skills, in-house. Here, the best of the old craft is married with the new: laser-precision, computer-controlled machinery used in concert with the brand’s original wooden hand tools. Every idea always begins with a sketch, but with each new movement (and there have been more than 1,000) many months, occasionally years of painstaking research and development leads to more than 500 Cad drawings per calibre. And only then can the machines swing into action – a carefully orchestrated symphony of parallel processes, which, every single day, must bring together hundreds of different parts from all over the factory onto the workbenches of Jaeger-LeCoultre’s 250-or-so watchmakers.
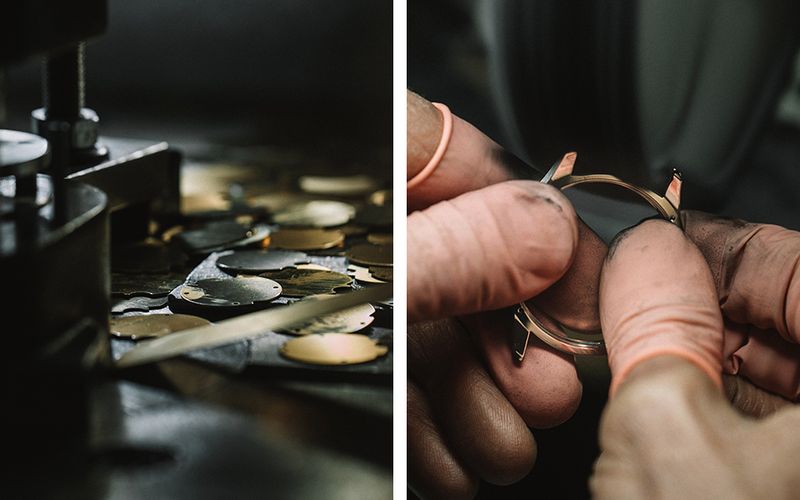
It’s not only the parts that need to be made – it’s the tools, too. They’re unique to each calibre, meaning between 60 and 100 new “swages” or punches must be forged for every new movement (the swage archive at Jaeger-LeCoultre clocks in at around 6,000 – quite a “stamp” collection). Under tonnes of downward force, more than 50 per cent of every movement’s components are punched from strips of steel or brass, then sent on for deburring and polishing.
Elsewhere, the machining rooms “profile turn” tiny parts from rods of raw metal, or mill them out robotically with drills manipulated by up to 14 axles. Programming these computer numerical control (CNC) machines is a laborious, manual process and can take a skilled operator a whole week when it comes to a particularly tricky part, such as the Gyrotourbillon’s spinning spherical cage, milled from a single piece of steel.
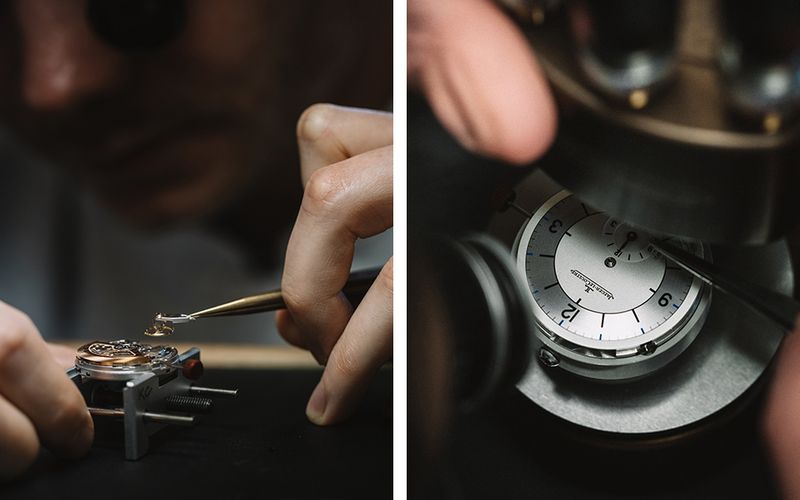
Upstairs from the fug of oil and hum of industry is where you’ll find the true hand-craftsmanship, busy at work. With an eye and a feel that takes years of apprenticeship to master, tiny synthetic rubies must be tweezered into pivot points, which hold microscopic drops of oil to ensure the smooth running of pinions. Even tinier rubies are set into the ticking anchor lever.
Elsewhere at the manufacture, the decorating atelier transforms raw metal into jewels. Every mainplate gleams with a “perlage” pattern, dotted on by hand using a spinning rod of rubber; every bridge is adorned with “Côtes de Genève” striping, applied with spinning wood, bringing coherence to every calibre’s maze of gleaming facets.
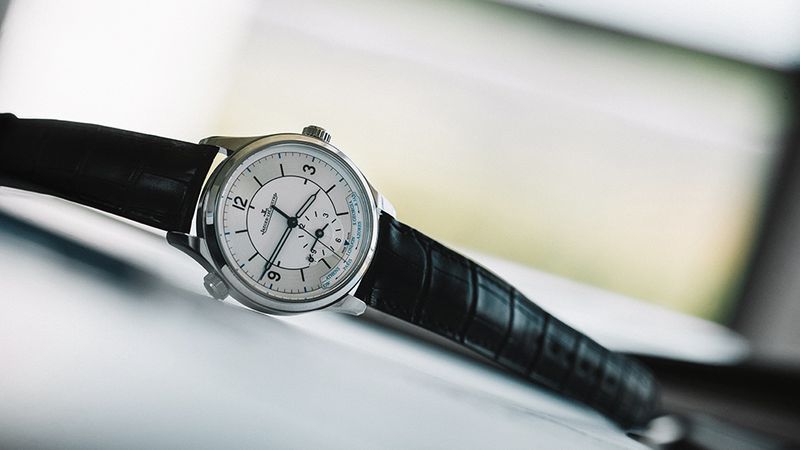
And then everything starts to come together – months since a lathe was turned in anger. The case is polished to a flawless sheen in a workshop sucked clean of dust, while upstairs, a master watchmaker pieces together the movement itself. With a professional satisfaction guaranteed every time, he spins the winding rotor with a flick of the hand, and the mechanics spring into life.
One thousand hours of rigorous testing later (some six weeks, for every watch that leaves the factory) and the quality control department can be satisfied: Jaeger-LeCoultre has created yet another masterpiece.