THE JOURNAL
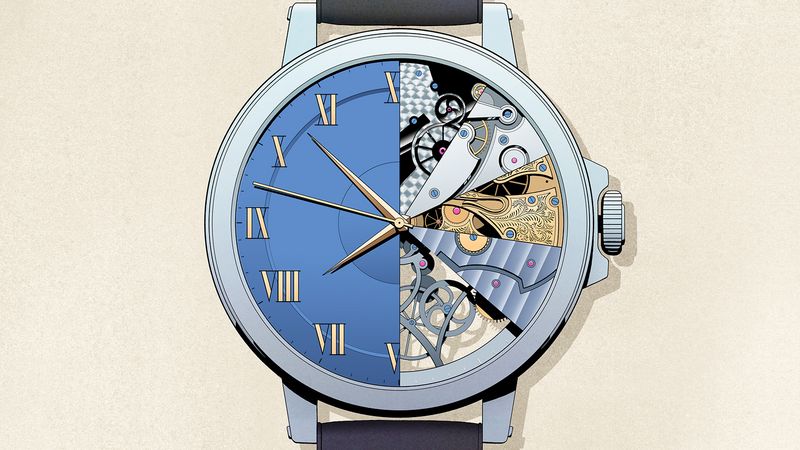
The techniques known today as “hand finishing” were developed by Swiss-French watchmakers in the 19th century, when all watchmaking was done by hand. As the name implies, finishing covers the final touches given to every part of the watch movement, whether visible or not. It takes hundreds of man-hours to make sure every angle, every surface represents the ultimate expression of the craft of watchmaking.
These days, following the introduction of sapphire casebacks through which this craft can be admired, you could be forgiven for assuming the finishing is purely decorative, but it’s a little more complicated than that. Advances in machining mean you can make a perfectly functional and handsome movement with no manual finishing whatsoever (and given the time and cost involved in doing it by hand, on watches priced below about £5,000, that is usually what has happened). But there are practical origins to a great many finishing techniques, too. For example, superior polishing of the mainspring, barrel and barrel cover improves the smooth transition of power to the movement and, by extension, the efficiency and accuracy of your watch.
The best watch brands pride themselves on finishing movements by hand partly as a means of preserving traditional crafts, but also because, done properly, it is impossible or impractical to replicate the highest standards of finishing by machine. Taking the time to train the craftspeople required and invest significant energy into each watch (sometimes as much as 40 per cent of the time needed to produce a watch goes into the finishing) is a mark of an elite watch brand. Indeed, some of the industry’s most demanding certifications of quality, such as the Poinçon de Genève, demand it. Here are some of the most commonly used finishing techniques in watchmaking.
01. Anglage
This is the technique for eliminating the edges between the flank of a piece and its surface. You’ll hear “bevelling” and “chamfering” used interchangeably, but technically it is only a chamfer when the angle is at 45 degrees. This polishing process removes any residual burrs left on the pieces after being cut out by machine, which would prevent the smooth running of the movement. It also limits corrosion. It is possible to smooth the outer angles chemically or mechanically with brushes, however, the interior angles, where two bevels meet at an acute angle, have to be done by hand. Some more difficult parts take 10 hours’ work, using tools with increasingly fine abrasives until the desired shine and angle are achieved. The ultimate anglage, mastered by only a few, is a wide edge with a convex cross-section, rather than flat. Again, a result only achievable by hand.
02. Black, mirror or specular polishing
Used sparingly for a high-impact, high-contrast effect on the finest movements, often on the hammers of a minute repeater or a tourbillon bridge. As its names suggest, it is a form of polishing that renders the part entirely free of scratches to leave a mirror-like surface that, depending on the angle light is reflected off it, appears to be black, grey or white. Parts can be prepared by using abrasive papers or by a machine-lapping method, but the final polishing has to be done by hand with a fine diamond paste to achieve that mill-pond flatness. The finished piece must be placed in the movement immediately to avoid it getting scratched. It is incredibly time-consuming. A single part no more than 10mm across can take about two hours to polish.
03. Côtes de Genève
Probably the most recognisable finishing technique, this straight-line engraving seen on the visible surface of movements’ plates and bridges translates literally as “Geneva waves” (you’ll also see them called Glashütte stripes by German watchmakers). Despite rumours that they were used originally to trap microscopic dirt particles, it is now thought they are simply decorative. Never applied to functional surfaces, because it would remove too much metal and therefore impact on accuracy, they are most commonly done via semi-automatic or numerically controlled machines. Those brands that choose to stick to tradition use one of two methods. In the rectifying rule method, the part to be decorated rests on a wooden table with holes along the edges. The rectifying rule (essentially a wooden arm with a cutting edge) is then used to scratch the surface in a regular pattern. Or you get handy with a lathe and adopt a steady to-and-fro motion to make waves.
04. Skeleton
Today this term refers to any watch where only the bare bones of the movement are left and the dial removed. This is a bit misleading because it presumes that the movement was complete to begin with and bits were then cut away. However, most modern skeletons were built from bare bones and were never whole, which is why those who practise the true hand craft of skeletonisation prefer the term “open working”. After the open-worked design is drawn, small holes are made in the metal, into which the watchmaker inserts the blade of a small handsaw and begins to cut straight through, trying not to slant the blade. After all the pieces are removed, the edges then need to be filed, bevelled and possibly decorated. The epitome of open working is the balance cocks on verge escapements from the 18th century – miniature works of art that feature open work with flower and leaf patterns and even faces.
05. Hand engraving
Two options here – the pattern is either an innie or an outie. The first option requires the engraver to sketch the motif on the surface to be decorated, which is then created by incisions into the material. About 20 different gravers are used to achieve differing depths of incision as well as straight and curved lines. Once the design is complete, its surface is burnished. For the outie method, the metal is pushed back by striking a chisel with a hammer. An engraver who works with this method will have made their own tools, specifically adapted to their hand and techniques.
06. Perlage
Also known as circular graining, spotting or stippling, this is one of the most widespread forms of finishing and is now purely for decoration. These tiny circles are seen on bridges, plates and the bottoms of dials of more or less every haute horlogerie movement. Originally created using an ivory rod turned by hand over the surface of the part, covered with sanding powder or a damp paste, it is now achieved by spinning abrasive pads fitted to a stippling machine. The turning rod is brought down onto the surface by hand to make the marks. This is one craft that is more difficult than it looks. You need steady, sensitive hands to make patterns that symmetrical.
07. Blued screws
One of the oldest decorative techniques is to provide a sprinkling of colour by blueing the screws that hold the movement together. They may all share a colour, but not all screws are blued equally. In a lower-cost movement, the screws will have been turned this shade chemically. If you’re paying a substantial sum, the blue colour is the result of heating each screw by hand, a process that not only colours it, but makes it harder and more resistant to corrosion. The skill here is in achieving a uniform colour, which requires the part to be polished and cleaned until no grease or dirt remains. Once it has been cleaned, it is then heated over a flame, inside an oven, with a heat gun or on top of an electric heater to between 288 and 310°C, depending on the shade of blue you’re after. English, Swiss and German watchmakers all favour a slightly different colour. Judging when to remove it from the flame is a precise art, as the colour will continue to darken for a second or two afterwards. If the steel goes past the desired blue into violet or even brown, the screw has to be repolished and cleaned before the process is attempted again.
Illustration by Mr Michael Kirkham