THE JOURNAL
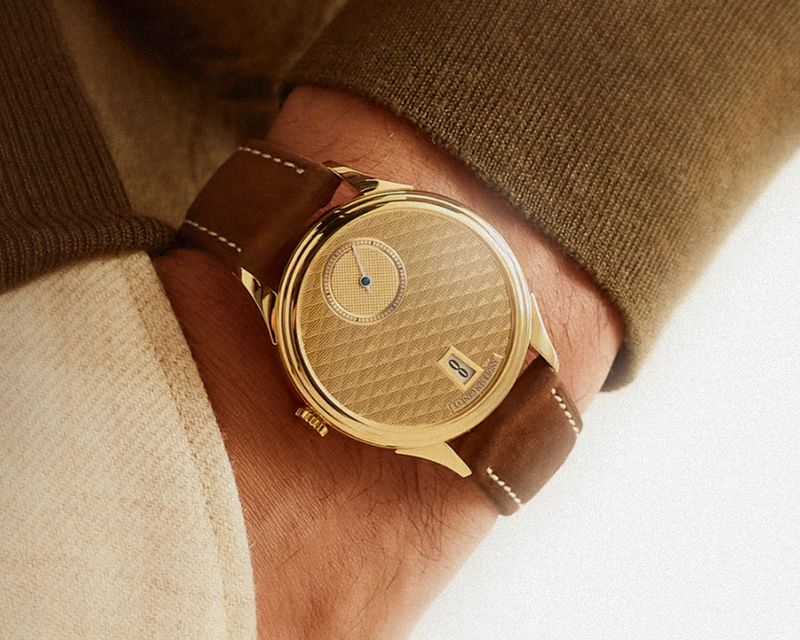
There’s a reason why the finest vintage watches can express a kind of individuality and warmth that’s hard to find in their modern equivalents. It’s not just down to the design, the backstory, nor the imperfections of age, though these can be intrinsically charming. Rather, it’s the sense of something fashioned with fingers, not machines. Decades ago, the cases of the finest watches were handmade and lovingly finished by specialised jewellers; lugs were delicately soldered on; dials and hands fashioned and decorated via arcane, analogue processes.
Today, in an industry demanding higher volumes and photo-exact replication, there’s less room for such unhurried, ultra-skilled approaches. Unless, that is, making tiny numbers of singular, acutely crafted watches is exactly what you’re all about.
Such is the case with Andersen Geneve, a small company based in workshops overlooking the Rhone River in central Geneva, where it turns out barely 50 wristwatches per year – most of them customised, several completely bespoke and all of them exquisite. In more than four decades, Andersen Geneve has made little more than 1,500 finished watches; Patek Philippe makes some 68,000 a year.
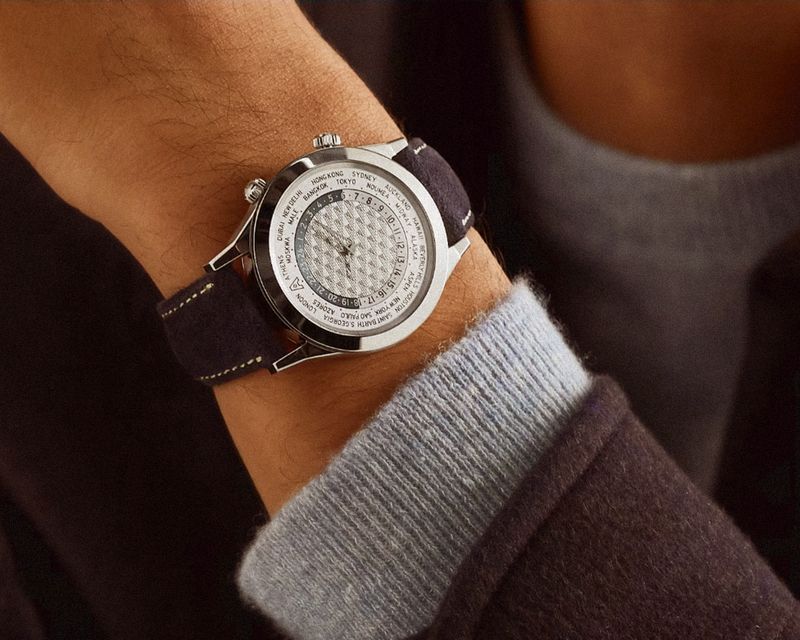
“The 1950s was the golden era,” says Mr Pierre-Alexandre Aeschlimann, Andersen Geneve’s managing director. “The designs were sober and elegant. They had no computers; no CNC milling or Cad design. The way they made the cases, the way they made the dials – when you look at it under the microscope, the proportions are right, the balance of the watch is right, and the sensitivity is right in a way that’s completely different to what you see today. That’s the watch we want to deliver.”
By way of example, one need look no further than the trio of sumptuous (and customisable) watches newly made by Andersen Geneve for MR PORTER. Two are versions of the company’s Tempus Terrae world timer, showing 24 time zones all at once, in white gold and yellow gold (both case and dial) respectively.
The third is a supremely elegant take on the rare “jumping hours” complication, also in yellow gold. The hour is shown in a window at the top of the dial, while a subdial at the bottom gives the minutes. The rest of the golden dial space is given over to a virtuoso display of guilloché engraving, an engine-turning technique that is one of watchmaking’s most cherished traditional art forms.
“There’s no electricity involved: it’s a human being, so it’s incredibly time-consuming and precise”
“We call it a ‘magic lozenge’ pattern,” Aeschliman says of the complex guilloche motif that’s repeated across the dial and winding rotors of all three watches, explaining that making a single such dial can take days. “The engraver has to use three different machines, which have to be calibrated perfectly. There’s no electricity involved: it’s a human being who is making the machines run, so it’s incredibly time-consuming and precise.”
Besides the four talented watchmakers at its Geneva HQ, who assemble the watches and fashion the complications and modules that make these mechanical works of art possible, Andersen Geneve’s strength is in the network of independent artisans – enamellist, engravers, case-makers, makers of hands and dials – spread out through Switzerland’s watchmaking heartlands, that it’s able to call on.
“We work only with the best of the best, and it depends on each project who we work with,” Aeschlimann says, explaining just how extreme the tolerances of handcraft involved can be. “A tenth of a millimetre variation on a lug is crucial, and for a dial it’s even more insane. Those kinds of details are my nightmare, and also my paradise.”
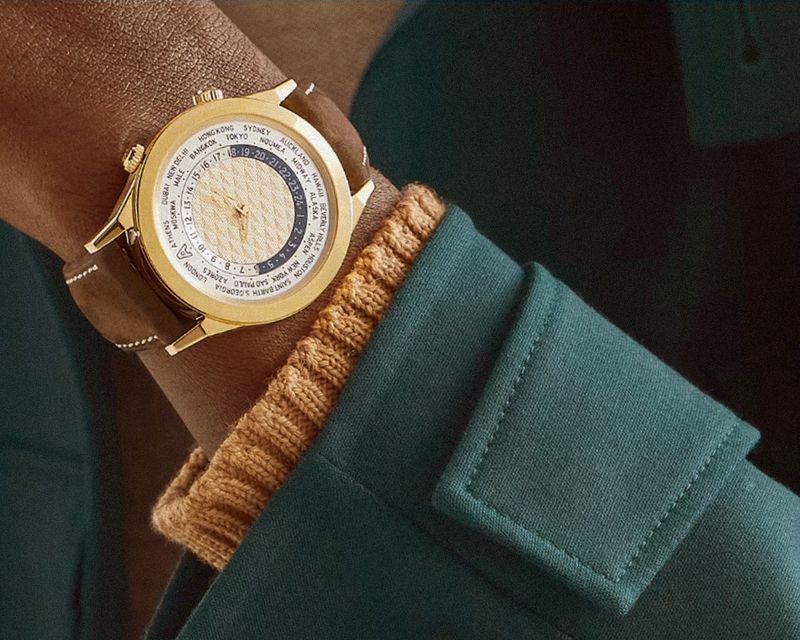
Given that Andersen Geneve stands for skills and techniques synonymous with the highest traditions of Swiss watchmaking, there’s some small irony in the fact that it was founded not by a Swiss watchmaker, but by a Dane. Mr Svend Andersen, born in Denmark in 1942, arrived in Switzerland in the 1960s. He made his name with a most remarkable invention: the Bottle Clock, a horological take on the ship-in-a-bottle tradition. The clock was completely assembled through the neck of the glass bottle, an achievement for which he gained international attention.
Subsequently, Andersen spent nine years employed in the Grand Complications department of Patek Philippe, honing his skills while working on the brand’s most important timepieces. In particular, he developed a fascination for the world timer watches that Patek Philippe had pioneered in the 1930s. This would become a signature of his own watchmaking, and so it remains for Andersen Geneve today.
Mr Andersen finally went it alone in 1980, establishing a studio to make bespoke (and often highly original) watches for an ever-growing coterie of international clients. In the process, he became something of a godfather figure within independent watchmaking, not least for his co-founding in 1985 of the influential Académie Horlogère des Créateurs Indépendants (AHCI), an organisation that champions artisanal watchmakers in Switzerland and around the world.
“Things take time. But that’s the beauty of it. No corners cut”
Having turned 80 this year, Mr Andersen is now semi-retired, though he’s still often to be found in the workshops of the company he founded. Famed for creations like his erotic watches with – ahem – adult-themed mechanical animations, and a secular perpetual calendar that needs no adjusting for the next 2,000 years, Andersen is particularly on-hand to advise on the most complex commissions, which can involve months of knotty problem-solving.
That’s because, at the heart of Andersen Geneve’s watchmaking is the notion that anything is possible, and nothing is off the table. From basic customisation of existing models – a different dial pattern, for instance, or the tweaking of the city ring on a world timer – to completely bespoke watches of high complexity. For those projects, the waiting time can be a year or more, but the results, inevitably, are worth it – and unique.
“Because you’re working with humans, you take into consideration that things take time,” Aeschlimann says. “But that’s the beauty of it. No corners cut. And everything we work on, we know who is getting the watch we’re making. That’s special, and that’s exclusivity.”